The demands on new batteries are constantly increasing, particularly in terms of their energy density. They also need to be lightweight, robust, safe, sustainable and cost-efficient in serial production. This is made possible by a complex synergy of mechanical design, electro-technical layout and customised software. Dr Stephan Horras, Head of Battery Development at EAS Batteries, answered four questions about the opportunities of modern battery development:
What are the core challenges of customised battery development?
"Every battery has its own requirements. They are determined by the planned application, regulatory requirements, the availability of suitable components and the properties desired by the customer. All of these parameters are collected in a specification document and checked for feasibility. The most important point here is to find an available cell with the right energy density that we can arrange and connect within the specified dimensions of the planned battery system. If there is no suitable solution on the market, we have to modify the requirements for the cell and therefore also the battery properties. Alternatively, we can offer to develop a new cell. As soon as a suitable cell has been found, we look which technology readiness level (TRL) the customer needs for his system. If the battery is only used for a feasibility demonstration, an electrical model that does not have to fulfil any special standards is sufficient. If the battery needs to be ready for series production, we include the necessary certifications and tests in the development process. The application-specific regulatory standards are the real technical challenge for us, as they usually form a tight corset. However, the biggest pressure to perform lies in developing the battery systems at ever lower production costs."
Which battery characteristics controls the mechanical design?
"Essentially, the mechanical design must ensure that the cells and the electrics are securely fastened in the battery housing. Components such as screws or nuts must not come loose, even when subjected to shock or vibration. The range between the various applications is wide. Under normal operating conditions on a ship, the battery is permanently exposed to small vibrations. During the various ignition phases of a space rocket, on the other hand, it has to withstand explosive shocks of up to ten thousand g, that is ten thousand times the acceleration due to gravity. The housing must also be able to withstand these stresses and, if necessary, have other properties - such as being impermeable to water or dust. The mechanical design must therefore also take the thermal design into account. If the housing is sealed, the heat generated during charging and discharging cannot be dissipated via ventilation. In this case, the battery requires liquid cooling. The manufacturing processes resulting from the mechanical design are also particularly relevant for clients. Here, the demand is growing that the batteries can be manufactured in series production with as few work steps as possible and with as much automation as possible. In this way, we use the mechanical design to control the robustness of the battery systems and their cost efficiency, taking into account the weight specifications. This is also where we have the strongest levers for making the battery sustainable. For example, it is important for recycling that the battery can be disassembled into its individual parts at the end of its life cycle. It is important to avoid gluing components. "
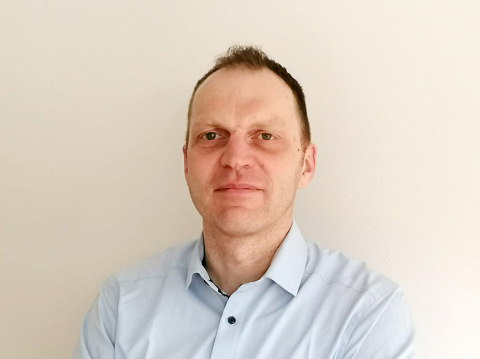
What influence does the electrical system have on the characteristics of the battery?
"The battery management system (BMS) is the core component of the electrical system. The so-called contactors and various sensors are connected to the electronic circuit board. The sensors determine how high the charging current, voltages and temperatures are. The contactors open and close like electronic switches when required. This is also where the so-called insulation monitor is located, which switches off the battery if the insulation falls below the minimum insulation threshold. All these components serve to ensure battery safety. Depending on the battery's safety level requirements, we install additional fuses that trigger in the event of overcurrent. Due to the large number of small components, we also have the most detailed options for optimising the cost efficiency of the battery in the electrical system. There is often a wide price range on the market for comparable components. It is also important that the electrical requirements are always ideally met and that no oversized elements are installed. This in turn also has an effect on the weight of the battery. We coordinate the individual components so that they achieve the optimum of the desired properties in the overall picture."
What function does the software of a battery system fulfil?
"When we talk about the software of a battery system, we are essentially referring to the software of the battery management system. The BMS primarily serves the safety of the battery, as it monitors its cells and balances out different states of charge. The more precisely we adapt the algorithm of the software to the cell, the more precisely, efficiently and safely the BMS works. The information is transferred to a graphical user interface via a data interface. It displays the state of charge and the so-called 'state of health' of the cells. Depending on requirements, other parameters can also be displayed, such as the temperature of the cells. In the future, a BMS will also be able to provide valuable data for more sustainable battery utilisation."
Read more about battery management systems of the future - opportunities and challenges.